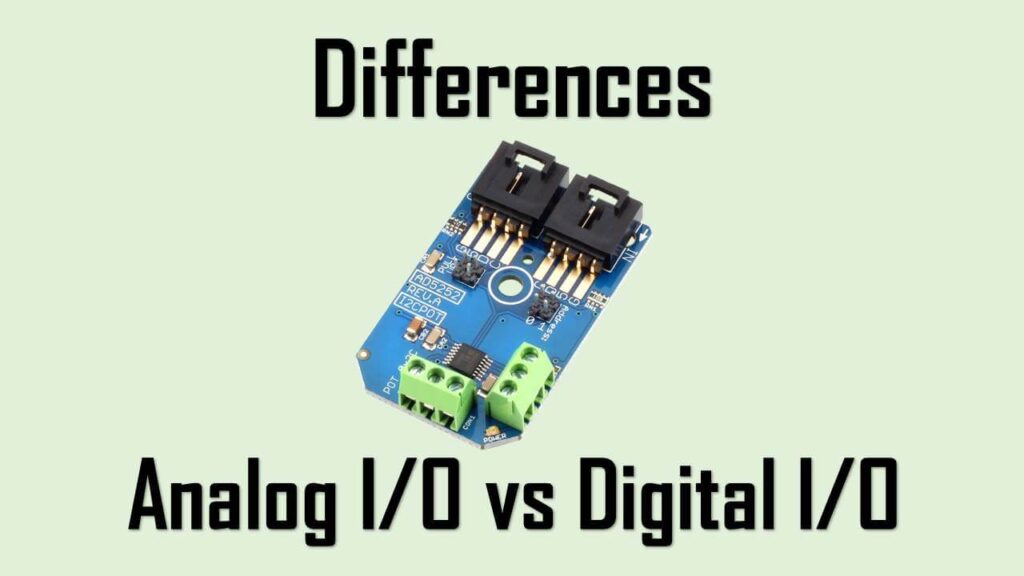
In today’s interconnected world, technology has become an integral part of our lives. From simple home appliances to complex industrial processes, every device operates on a set of instructions that control its behavior. These instructions are facilitated by Input/Output (I/O) modules, which enable communication between the digital and analog realms.
In this article, we will delve into the world of Digital and Analog I/O modules, exploring their functions, applications, and the differences between them. Whether you’re a technology enthusiast, a student, or a professional in the field, this comprehensive guide will shed light on the fascinating world of I/O modules.
What are Digital and Analog I/O Modules?
To begin, let’s understand what Digital and Analog I/O modules are:
Digital I/O Modules
Digital I/O modules serve as the interface between digital devices (such as microcontrollers or computers) and external peripherals, sensors, or actuators. The term “digital” refers to a discrete signal that can have only two values: 0 (low) and 1 (high). These modules are designed to process binary data, making them highly efficient for applications requiring simple on/off control or data transmission.
Analog I/O Modules
On the other hand, Analog I/O modules are responsible for bridging the gap between analog devices and digital systems. Unlike digital signals, analog signals are continuous and can take on a range of values within a specified range. Analog I/O modules convert the varying analog signals from sensors, transducers, or other devices into digital data that can be processed and manipulated by digital controllers or computers.
How Do Digital I/O Modules Work?
Digital I/O modules consist of input and output ports. Input ports receive signals from external devices, while output ports send signals to control external devices. Here’s how they work:
Input Functionality
When connected to sensors or other digital devices, the input port of a Digital I/O module detects changes in voltage levels. If the voltage exceeds a specified threshold, it registers a logical high (1); otherwise, it registers a logical low (0). These binary signals are then processed by the connected controller to make decisions or trigger actions.
Output Functionality
The output port of a Digital I/O module sends control signals to external devices, such as turning on a motor, activating a relay, or controlling a light switch. When the connected controller sends a logical high (1) to the output port, the module supplies power to the external device, and when it sends a logical low (0), power is cut off.
Applications of Digital I/O Modules
Digital I/O modules find widespread use in various applications due to their simplicity and reliability. Some common applications include:
Home Automation
In home automation systems, Digital I/O modules are employed to control lighting, heating, ventilation, and air conditioning (HVAC) systems, security cameras, and other smart home devices.
Industrial Automation
In industrial settings, these modules are used to control conveyor belts, motors, pumps, and monitor safety switches or emergency stop buttons such as the IA-3174-E.
Robotics
Digital I/O modules play a critical role in robotic systems, where they control movements, grippers, and interact with various sensors to make decisions.
IoT (Internet of Things)
In IoT applications, Digital I/O modules facilitate communication between connected devices, enabling them to respond to commands from the cloud or other remote systems.
How Do Analog I/O Modules Work?
Analog I/O modules are more complex than their digital counterparts as they deal with continuous signals. Here’s how they function:
Analog-to-Digital Conversion (ADC)
The first step in the operation of an Analog I/O module is analog-to-digital conversion. The module takes the varying analog input voltage from sensors or devices and converts it into a digital value using an ADC. The ADC samples the analog signal at regular intervals and quantizes it into discrete digital values.
Digital-to-Analog Conversion (DAC)
Conversely, when an analog output is required, the module utilizes a Digital-to-Analog Converter (DAC). The DAC takes a digital value from the connected controller and converts it back into an equivalent analog voltage or current signal. This allows the module to control analog devices like variable speed drives, proportional control valves, or other analog actuators.
Applications of Analog I/O Modules
Analog I/O modules have a wide range of applications where precise measurements and continuous control are crucial. Some common applications include:
Process Control
In industrial process control, Analog I/O modules are utilized to monitor and adjust parameters such as temperature, pressure, flow rate, and level.
Data Acquisition
For scientific research and data acquisition systems, Analog I/O modules are essential for capturing analog signals from sensors and converting them into digital data for analysis.
Audio and Video Processing
Analog I/O modules are extensively used in audio and video processing systems to handle the continuous signals and convert them into digital format for transmission and storage.
Medical Instrumentation
In medical devices like heart rate monitors, blood pressure monitors, and electrocardiograms (ECG), Analog I/O modules are responsible for converting vital signs into digital data.
Differences between Digital and Analog I/O Modules
Now that we have explored the workings and applications of both Digital and Analog I/O modules, let’s highlight some key differences between the two:
Signal Type
The primary difference between Digital and Analog I/O modules lies in the type of signals they process. Digital I/O modules handle binary signals, while Analog I/O modules process continuous signals.
Precision and Resolution
Analog I/O modules typically offer higher precision and resolution due to the continuous nature of analog signals. Digital I/O modules, on the other hand, are limited to discrete values, which can lead to reduced precision in some applications.
Complexity
Analog I/O modules are generally more complex and require additional components, such as ADCs and DACs, to convert analog signals to digital and vice versa. Digital I/O modules are simpler as they deal directly with binary signals.
Noise Immunity
Digital I/O modules are more immune to noise and interference since they rely on binary signals with clear voltage thresholds. Analog signals are more susceptible to noise, requiring additional measures to filter and stabilize the data.
Conclusion
In conclusion, Digital and Analog I/O modules serve as the crucial link between digital controllers and the analog world of sensors and actuators. Digital I/O modules handle binary signals, providing simplicity and reliability in various applications, while Analog I/O modules cater to continuous signals, enabling precise control and measurement.
Both types of I/O modules play indispensable roles in modern technology, shaping our homes, industries, and the digital landscape as a whole. As technology continues to evolve, understanding the nuances of Digital and Analog I/O modules becomes increasingly vital for engineers, developers, and enthusiasts to build innovative and efficient systems.
So, the next time you switch on a light or control a robot, remember the vital role of I/O modules, connecting the binary and continuous worlds in harmony.